Compliance Testing
NABL Accredited and ISO/IEC 17025 Compliant Laboratory
RSL Compliance testing
RSL compliance testing refers to a process where a product is tested to ensure it complies with a “Restricted Substances List” (RSL), which is a list of chemicals or substances that are restricted or banned from being used in a product due to potential health or environmental concerns; essentially, it’s a method to verify that a product does not contain harmful chemicals exceeding allowed limits, often used in industries like textiles, apparel, and electronics to meet regulatory standards and brand requirements.
Key points about RSL compliance testing:
RSL testing helps companies ensure their products are safe for consumers, comply with relevant regulations, and maintain a good reputation by managing chemical risks throughout the supply chain.
Manufacturers, retailers, and brands often require their suppliers to undergo RSL testing to demonstrate compliance with their standards.
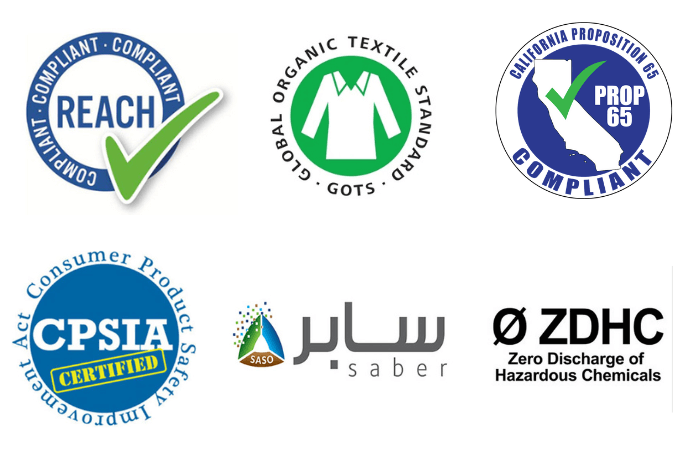
Ecological laboratories offer compliance testing for a wide variety of materials and products, including:
- Bags and accessories
- Clothing
- Electrical and electronic equipment
- Food contact materials and articles
- Footwear and leather products
- Home furnishings
- Home textiles
- Houseware items
- Jewellery
- Pet products
- Sports and leisure items
- Sunglasses
- Toys and juvenile products
- Textile auxiliaries
- Cosmetic formulations
- Dyes and pigment products
- Paints etc
CPSIA
Children’s toys / products sold in US Market comply with the US Consumer Product Safety Improvement Act (CPSIA) of 2008. The children’s products are any product designed or intended primarily for use by children aged 12 or younger.
US manufacturers and importers are required to test children’s products to ensure they do not contain hazardous substances, including lead and phthalates, and that they also comply with other toy safety requirements.
California Proposition 65
CA Prop 65 compliance relates to the Safe Drinking Water and Toxic Enforcement Act, 1986, a California law established to promote clean drinking water and warn the public about the presence of toxic chemicals in consumer products and environment.
The Prop 65 list contains approximately 900 chemicals “known to the state to cause cancer, birth defects or other reproductive toxicity”. This list is updated at least annually. Prop 65 affects all consumer products sold or distributed in California, including textiles, footwear, hard goods, DIY products, toys, juvenile products, stationery, electrical/electronic items and more.
ROHS ( Restriction of hazardous substances )
The RoHS2 Directive, 2011/65/EU, restricts the use of 10 potentially hazardous substances including Heavy metals as Lead Cadmium, Mercury Chromium VI, four phthalates and flame retardants as PBBs and PBDEs in electrical and electronic products.
RoHS limits these substances to 0.1% or 1,000 ppm (except for cadmium, which is limited to 0.01% or 100 ppm) by weight of homogenous material.
Global Organic Textile Standard (GOTS)
GOTS standard defines requirements to ensure organic status of textiles, from the raw materials, through environmentally and socially responsible manufacturing up to labelling in order to provide a credible assurance to customer. They apply to all textile products including
yarns, fabrics, clothes, home textiles, personal hygiene products as well as food contact textiles .
All above textile articles and even chemical inputs used in process cycle are assessed to meet GOTS restricted substances criteria.
LWG Chemical Management
LWG (Leather Working Group) was formed in 2005 to assess and control the environmental impact of leather production at tanneries.
One of the main aims of LWG Leather Manufacturer Audit a sustainability standard is to Improve Hazardous chemical management and increase use of non-hazardous chemicals in leather industry from tanneries to consumer goods.
AFIRM
The AFIRM (the Apparel & Footwear International RSL Management Working Group) provides resources for sustainable , self-governing RSL implementation.
The AFIRM testing matrix applies a risk-based approach to testing. AFIRM (Apparel and Footwear International RSL Management) is a brand-driven membership organization of apparel and footwear companies collaborating to promote chemicals management in the global supply chain.
Zero Discharge of Hazardous Chemicals. Foundation’s MRSL ( manufacturing restricted substances ) is a list of chemical substances that are banned from intentional use in processing textile materials, leather, rubber, accessories etc used in textiles, apparel, and footwear.
Using chemical formulations that conform to an MRSL allows suppliers to assure themselves, and brands, that banned chemicals are not used during manufacturing processes.
The control of restricted substances in the inputs, reduces the risk of effluent and waste discharge containing harmful and hazardous substances and helps avoid environment pollution.
REACH EU REACH Compliance and Testing
REACH compliance testing analyses presence of harmful substances found on Annex xvii and candidate list of SVHC.
The purpose of REACH Annex XVII is to place restrictions upon harmful chemicals in consumer products. There are currently 70 entries under Annex XVII, each with its own specific restrictions, and suppliers of consumer goods have a legal obligation to ensure that their products are compliant with any limits laid down in these restrictions.
If a chemical is present in any concentration and is listed on Annex XVII, it would banned from the EU market.
SVHCs require authorization to be used in any product and are generally allowed if the concentration is less than 0.1% of the total product weight. If the concentration is higher, the importer or manufacturer must disclose this to customers with correct labeling and to ECHA, and may be subject to restriction.